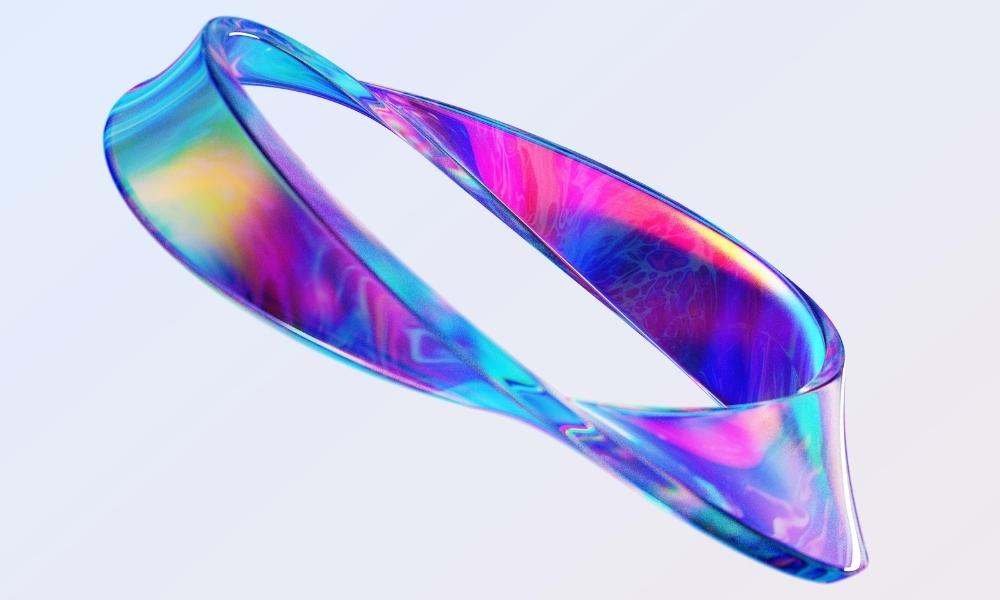
Velocità, qualità e basso costo sono i traguardi da sempre considerati da quando c'è competitività nel mondo degli affari.
Il Lean Six Sigma si è rivelato fondamentale perché consente di lavorare su tutte e tre le variabili contemporaneamente unendo due filosofie:
- La Lean, che ha il suo focus principale sulla velocità di processo.
- Il Six Sigma che ha punta alla qualità di processo.
Chiaramente non si tratta di processi banali e l'implementazione di queste metodologie si basa prima di tutto sulla percezione che ci sia bisogno di un cambiamento.
Solo dopo, si richiede un cambiamento culturale importante e alla fine intervengono formazione e applicazione di strumenti.
Ci sono aziende che hanno provato ad adottare o una strategia di tipoLean o Six Sigma escludendone una o consentendo anche le due di competere ed emergere. Tuttavia, se ci si limita a considerarle come due pratiche di competizione si perde completamente il senso di quanto possano essere efficaci insieme: non si può raggiungere la massima velocità senza aumentare anche la qualità e non è possibile raggiungere la massima qualità senza aumentare la velocità.
Pertanto, in prima battuta, procediamo con l’analisi di "Six Sigma".
Cos'è il Six Sigma?
La denominazione Six Sigma indica un programma di gestione della qualità basato sul controllo della varianza, (indicata con la lettera greca Sigma) che ha lo scopo di portare la qualità di un prodotto o di un servizio ad un determinato livello.
Questo tipo di programma è stato ideato da Bob Galvin e Bill Smith a metà degli anni '80 e introdotto per la prima volta dalla Motorola, successivamente si è diffuso ad altre importanti compagnie come General Electric, Toyota, Honeywell e Microsoft.
Secondo gli standard Six Sigma, le aziende dovrebbero raggiungere un tale controllo del processo da avere soltanto 3,4 parti difettose per milione il che porta a limiti molto restrittivi sulla variabilità del processo produttivo.
Ma si può davvero raggiungere un livello del genere?
La tua prima reazione sarà sicuramente stata: "è impossibile!"
In realtà, sebbene vari casi aziendali dimostrino che sia raggiungibile, non ci si deve soffermare alla sola lettura del numero.
Le aziende, infatti, adottano la metodologia Six Sigma al fine di individuare i processi che consentano di focalizzarsi sull’eliminazione dei difetti e degli sprechi piuttosto che sul miglioramento della prestazione media, così da implementare nuovi sistemi di gestione.
Non a caso il purpose del Six Sigma, semplice ma potente, è "i risultati di un qualunque processo sono il risultato di quello che entra nel processo".
Significa che prima di iniziare a migliorare i processi, si devono individuare le variabili che influenzano il risultato. Nel parlato comune diremmo "ricercare le cause alla radice".
Dal punto di vista operativo il Six Sigma non è altro che un'applicazione rigorosa di tecniche statistiche e principi di qualità, fortemente orientata al raggiungimento dell’obiettivo ed efficiente.
La metodologia integra alcuni metodi e direttive della qualità aziendale "tradizionale", puntando a renderli più efficaci con lo scopo di giungere ad una performance globale pressoché esente da difetti.
Applicazione del metodo DMAIC
Il Six Sigma utilizza un pattern ciclico chiamato DMAIC:
- Define - Definire: in questa fase il gruppo di lavoro deve:
-
- Identificare il processo o prodotto da migliorare.
- Tradurre i bisogni del cliente in requisiti (detti anche CTQ - Critical to Quality).
- Identificare i partecipanti necessari per il progetto.
- Sviluppare una pianificazione di alto livello.
Al termine solitamente si richiede alla direzione l’approvazione a procedere.
- Maesure - Misurare: questa fase consiste nella valutazione del livello attuale di prestazione del processo o prodotto relativamente ai requisiti individuati. Occorre prima di tutto individuare e validare un adeguato sistema di misura e solo dopo effettuare la misura. Infine, per confronto dei risultati con gli standard richiesti, si può calcolare l'attuale livello di sigma. In risposta a questo obiettivo, si fa ricorso tipicamente alla statistica descrittiva e al campionamento.
- Analyse - Analizzare: in questa fase, sulla base dei dati misurati, si applicano le tecniche statistiche per individuare le cause dei difetti e poter quantificare in che misura ogni causa (o l'interazione tra più cause) influenza il requisito studiato e la sua varianza. Gli strumenti utilizzati sono numerosi, alcuni tra i più comuni sono qui elencati:
-
- analisi della varianza
- istogramma di Pareto
- regressione
- correlazione
- stratificazione
- Improve - Migliorare: in questa fase in cui si propongono e si mettono in pratica i miglioramenti, solo dopo aver compreso chiaramente le cause dei difetti. È infatti una prerogativa del Six Sigma quella di evitare che si arrivi immediatamente alle soluzioni. Occorre invece creare un ventaglio di possibili soluzioni agendo direttamente sulle cause più importanti, effettuando un’analisi di costi e benefici ed infine, valutando la necessità e le modalità di eventuali esperimenti o test pilota. Gli strumenti generalmente utilizzati per selezionare la soluzione migliore, generalmente, sono:
-
- FMEA (Failure Modes and Effects Analysis).
- DOE (Design of Experiments - Progettazione degli Esperimenti).
- Analisi costi-benefici.
- Control - Controllare: nella fase finale avviene il controllo continuo del processo al fine di standardizzarlo e stabilizzarlo. Si quantifica inoltre, l'entità del miglioramento e si intraprendono azioni di supporto come la redazione delle procedure definitive e l'addestramento del personale. Generalmente vengono utilizzati strumenti come i diagrammi di controllo e il piano controllo della qualità.
Facciamo un esempio
In conclusione, vi proponiamo un esempio pratico per comprendere meglio quanto discusso.
Immaginiamo di avere due macchine non identiche ma che possono essere impiegate per la produzione dello stesso componente (o meglio per realizzare una fase del ciclo di lavorazione). Diciamo che, dai dati raccolti finora, la lavorazione sulla prima macchina richiede mediamente 30 minuti, mentre la media sulla seconda macchina è di 35 minuti. Tralasciando il costo della lavorazione, che per semplicità diciamo essere uguale sulle due macchine, qual è la macchina che dovrebbe essere impiegata? La logica comune suggerisce semplicemente che è la prima, dato che in media richiede 5 minuti in meno di lavorazione. La logica Six Sigma invece impone di scendere maggiormente nei dettagli, dato che la media, da sola, non è un indicatore significativo per questo studio.
Qual è ad esempio il grado di precisione delle due macchine? Una produce più scarti o richiede più lavorazioni rispetto all’altra?
C’è anche un’altra indicazione, meno ovvia: dato che le macchine fanno parte di differenti cicli di produzione su numerosi articoli differenti e considerando che in condizioni normali le macchine potrebbero essere occupate da altre lavorazioni, qual è il tempo di "coda"? Detta diversamente: qual è la variabilità del tempo di attesa sulle due macchine?
Chiaramente se la prima macchina (quella su cui il tempo è inferiore) è la preferita anche su altri prodotti, il mix di produzione indirizzerebbe a portare a tempi di attesa mediamente più lunghi rispetto alla seconda macchina; i tempi di attesa potrebbero essere molto variabili. Tale variabilità potrebbe rendere nullo il vantaggio di tempo del ciclo di lavorazione!
Dall'esempio potrebbe sembrare che il procedimento sia molto complesso: nella realtà la metodologia Six Sigma fornisce delle indicazioni molto chiare e relativamente semplici sul percorso da seguire.
Il primo passo da compiere comunque è strutturare la raccolta dei dati e iniziare ad interpretarli in modo critico; infatti, l'impiego di KPI e dashboard aiuta significativamente il processo decisionale.
Iniziare un percorso Six Sigma potrebbe essere oneroso, soprattutto per prepararsi adeguatamente assumendo anche personale qualificato. Ne è un esempio il ricorso ad un consulente oppure la formazione del personale: vale il principio di "investimento".
In conclusione, l’applicazione della strategia Six Sigma può portare ad un vantaggio competitivo reale attraverso una maggiore consapevolezza, un maggior livello di servizio al cliente ed un minor impatto dei costi di qualità!