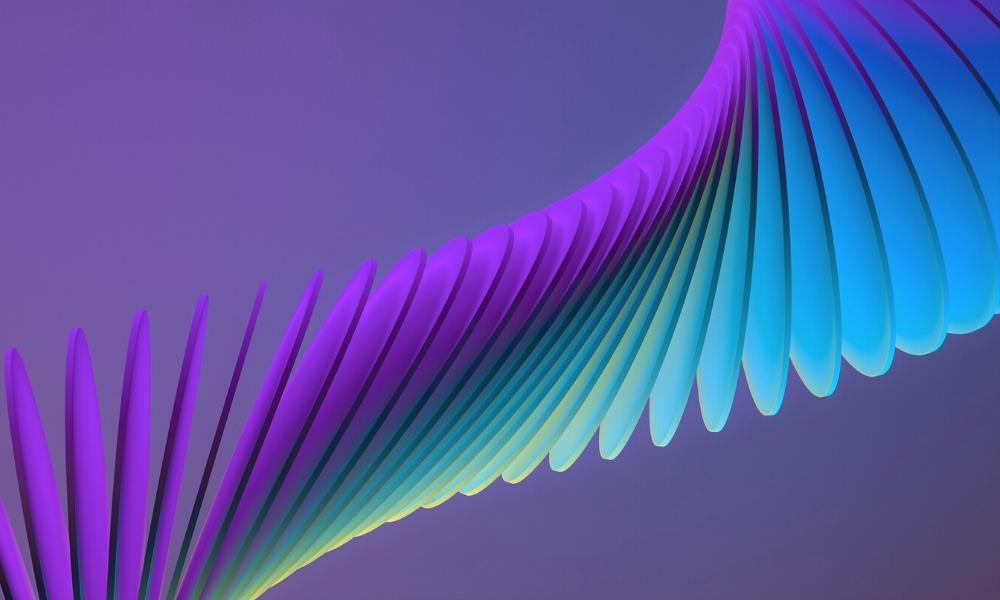
Adottare degli indicatori di performance è la scelta migliore che si possa fare per misurare e valutare le attività svolte.
Pensare di risolvere un problema che apparentemente si pone, ma che in realtà non esiste, è un grande spreco di tempo ed energie. Ma, soprattutto, il rischio di affidarsi all’opinione personale è quello di osservare solo ciò che è noto, conosciuto, familiare escludendo a priori dal mindset di valutazione tutto il resto.
Spesso occorre poter monitorare e misurare in modo tempestivo e frequente una determinata attività.
La falla è l'opinione personale in questo contesto, la soluzione invece è rappresentata dagli indicatori di performance, meglio noti in KPI.
Quali caratteristiche devono avere?
Tra i più diffusi vi sono gli indicatori economici-finanziari che presentano il grande limite di essere indicatori "a consuntivo" e di medio periodo.
Inoltre, per un'azienda che lavora a tempi sostenuti è necessario ottenere misurazioni tempestive e frequenti. Per questa ragione si deve evitare di avere troppi indicatori che potrebbero creare confusione e richiedere tempi lunghi per la loro analisi.
Alla luce di quanto affermato quindi è chiaro quanto sia indispensabile scegliere pochi KPI che siano possibilmente facili da implementare, gestire, analizzare. Chiaramente parlare di "facile" non è mai corretto. Infatti, l'implementazione di un sistema di monitoraggio potrebbe richiedere un certo sforzo iniziale, ma una volta assettato in modo corretto ed ottimale fornirà un dato aggiornato e consistente senza richiedere ore di elaborazioni.
Cerchiamo di capire quali sono e come utilizzarli.
Quali scegliere?
Esistono tante opportunità a costo contenuto e talvolta a costo zero:
- MES (Manufacrturing Execution System), il sistema informatico finalizzato alla gestione e al controllo della funzione produttiva di un'azienda.
- DCS (Distributed Control System) un insieme di hardware e software per la raccolta e l'analisi dei dati di produzione.
- SCADA (Supervisory Control and Data Acquisition) come il DCS ma solo software.
Nella scelta di uno o di un set di indicatori è fondamentale la padronanza. Affinché la scelta e la gestione sia ottimale è importante saperli gestire e comprendere a pieno le logiche algoritmiche che conferiscono loro valore.
Perché è importanti saperli padroneggiare?
Le ragioni sono varie:
- Se non si conoscono i driver di prestazione non si può aver chiaro quali eventi o circostanze migliorano o peggiorano il risultato. La conseguenza è che non si ha chiaro quali siano le azioni correttive o permanenti da applicare per aumentare la prestazione.
- La semplicità di comprensione deve essere anche condivisa dal personale operativo oltre che dal titolare o dal manager, per avere una situazione di equilibrio ed evitare di stagnarsi nello sterile concetto di "misurazione".
Sebbene l’ultimo punto suoni come una contraddizione, è importante ricordare che i KPI non devono diventare un sistema di votazione delle prestazioni individuali. Lo scopo di un indicatore e delle azioni che ne derivano è infatti quello di trovare soluzioni a problemi.
Vediamo nel dettaglio l'indicatore di performance più importante e diffuso, sviluppato dal Japan Insitute of Plant Maintenance (JIPM).
L’indicatore OEE overall Equipment Effectiveness
È uno dei KPI di performance più importante e diffuso, sviluppato dal Japan Institute of Plant Maintenance (JIPM) è adimensionale ed è espresso in percentuale. La sua natura sistemica permette di monitorare tre diverse variabili sulle quali è possibile focalizzarsi concentrando gli sforzi secondo le priorità derivate, ossia intervenendo per primo sull’indice con risultato peggiore.
L'indicatore OEE fornisce un'indicazione globale sulla capacità di un insieme di risorse di generare valore per il cliente (output) con le risorse produttive a disposizione (input).
Formalmente il calcolo dell’indicatore può essere sintetizzato come:
OEE = Disponibilità x Prestazione x Qualità
Nel dettaglio:
- Disponibilità: percentuale dell'effettivo tempo di attività rispetto a quello disponibile.
- Prestazione: percentuale di parti prodotte rispetto alla potenzialità teorica, quando l'impianto è attivo.
- Qualità: percentuale di parti conformi rispetto al totale delle parti prodotte.
Le cause che potrebbero abbassare il valore dell'indicatore sono generalmente sei, di carattere generale e raggruppate in tre categorie corrispondenti ai tre fattori dell'OEE.
- Le perdite per inattività sono misurate in unità di tempo. Esse includono:
- guasti e tempi di riparazione
- tempi di set-up e regolazione
- altre perdite causa di inattività - Le perdite di velocità sono misurate in unità di produzione, ricavate dalla differenza tra produzione reale e produzione potenziale. Per produzione potenziale si intende quella che si otterrebbe se le macchine lavorassero costantemente alla velocità standard ottimale per ogni prodotto.
- Le perdite per difetti sono misurate in unità di produzione. In questo caso il valore è ottenuto dalla differenza tra produzione reale totale e produzione che soddisfa le richieste dai clienti (prodotti conformi).
Di conseguenza si spiega il valore percentuale dell'indicatore e la sua rappresentazione grafica.
Un altro aspetto da considerare per la misurazione dell'OEE è la frequenza, nell'esempio sopra riportato la base di calcolo è il mese ma si tratta di un report annuale.
Sono frequenze giuste quelle settimanali, giornaliere o addirittura per singolo turno. Inoltre, avere chiara la situazione nel tempo permette di misurare la variabilità un tipo di indicazione che fornisce ulteriori informazioni sulle possibili cause di perdita e sulla bontà e malevolenza delle soluzioni adottate.
Quando l'indicatore OEE è buono?
Per rispondere a questo interrogativo si può partire da una formula di indicatore semplificata:
OEE = (Pezzi Buoni x Tempo Ciclo Standard) : Tempo Apertura Impianto
Nel dettaglio:
- Disponibilità: percentuale dell'effettivo tempo di attività rispetto a quello disponibile.
- Prestazione: percentuale di parti prodotte rispetto alla potenzialità teorica, quando l'impianto è attivo.
- Qualità: percentuale di parti conformi rispetto al totale delle parti prodotte.
Considerando questo esempio, in risposta all’interrogativo di cui sopra, un valore può essere considerato:
- Obiettivo oppure ottimale quando è intorno al 80-85%. Valori superiori possono essere raggiunti solo con azioni precise ed in contesti mirati (si pensi all'implementazione del WCM-Word Class Manufacturing).
- Incorretto nel caso di valore superiore al 90% e talvolta al 100% perché il risultato è il frutto di errori di impostazione del calcolo.
- Basso quando si aggira tra il 55-60%. Tipicamente è il caso delle aziende che non hanno mai intrapreso un percorso di miglioramento continuo.
La corretta applicazione di metodi e strumenti può incrementare il valore dell'indicatore anche in periodi relativamente brevi fino all'80 – 85%.
In altri termini, un incremento del valore dell'OEE, per esempio, del 25% corrisponde ad un incremento della produzione netta del 42% (25% - 60%): si produce il 42% in più a parità di risorse.
Cosa fare per analizzare le cause di mancata performance?
Per analizzare le cause di mancata performance (quando il valore dell'indicatore non è ottimale) occorre analizzarne le cause. Si costruisce quindi un deployment delle perdite e si applica la ben nota Legge di Pareto.
Creando un istogramma delle perdite, ordinato in modo decrescente, si costruisce la curva di Lorenz (distribuzione cumulativa) e si prendono in esame solo le cause, che sommate costituiscono l’80% delle perdite totali.
Nell’immagine riportata sopra vi un chiaro esempio di quanto argomentato. Si può notare infatti, come le prime 4-6 perdite rappresentino l’80% del totale della perdita di prestazione.
Seguire un'analisi dettagliata consente di risparmiare tempo ed energie, di affrontare i problemi contemporaneamente senza fissare un ordine di priorità.
Infatti ogni performance negativa necessita di tecniche, metodi e strumenti idonei alla sua risoluzione.