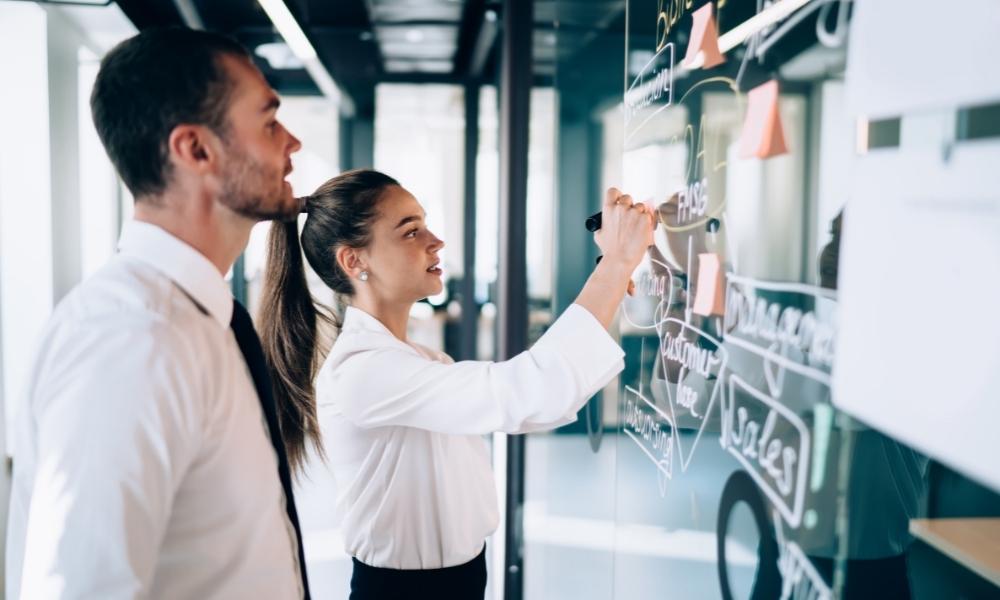
Spesso nei contesti aziendali, quando si parla di manutenzione, si percepisce l'associazione della parola ad un mero onere. Probabilmente perché interventi riparativi e migliorativi costringono a fermare le macchine e di conseguenza rallentare la produzione. Questo pensiero potrebbe essere vero ma è sicuramente inesatto. Cerchiamo insieme di fare un po’ di chiarezza. È vero che in linea generale le prestazioni di una macchina o di un impianto tendono a degradare nel tempo sia per obsolescenza che per mancata o inefficace manutenzione ma è al contempo vero che il peggioramento delle performance del congegno si traduce in interruzioni per guasti, problemi di qualità e micro-fermate.*
Tuttavia, è corretto affermare che un’adeguata politica manutentiva risolve quasi totalmente i problemi.
*Si tratta di una serie di fermi macchina di durata inferiore ad un certo valore. Queste ultime sono tra le più difficili da identificare dato che solitamente non vengono registrate puntualmente.
Cosa si intende per manutenzione?
La manutenzione è l’insieme delle attività che hanno come obiettivo quello di mantenere un elemento, macchina o sistema, nello stato in cui può assolvere alla propria funzione. Quindi, non si tratta di realizzare solo azioni tecniche correttive o di sostituzione delle parti guaste e usurate ma comprende anche l’efficiente organizzazione dell’attività stessa. Infatti, tra gli scopi principali troviamo:
- La minimizzazione dei tempi di diagnosi tramite mezzi e strumenti adatti.
- La riduzione del numero di fermate per i guasti casuali.
- L’aggregazione di scadenze e interventi.
- L’assicurare l’efficienza globale per lunghi periodi.
- La minimizzazione delle interruzioni programmate, la cui durata e cadenza risultino già previste e prestabilite.
Ovviamente, l’azione manutentiva non è unica ed universale. Per ogni congegno, dopo un’attenta analisi, ci sarà una soluzione migliore. È chiaro quindi che la scelta di quella migliore dipende chiaramente dalla valutazione di alcuni macro-fattori e di parametri tecnico-economici.
Tra le determinanti troviamo:
- La complessità e la dimensione dell’impianto.
- Il grado di conoscenza dello stesso e livello di maturità ed affidabilità delle tecnologie installate.
- La strategia aziendale.
Tra le considerazioni degli aspetti specifici concorrono:
- Il tasso di guasto, che misura la quantità di guasti che si sono verificati o che si possono verificare in un determinato periodo.
Non devono essere dimenticate inoltre una serie di voci di costo:
- Di manutenzione preventiva.
- Della pura attività di manutenzione.
- Indotto dal guasto.
- Di manutenzione accidentale (difficile da stimare).
- Di ispezione.
Quali sono i tipi di manutenzione?
Avendo chiarito cosa si intende per manutenzione e che non esiste un’unica azione che sia calzante per tutti i macchinari o impianti, chiariamo quali tipologie ci sono e cosa le distingue.
Manutenzione accidentale
È il tipo più diffuso ma anche il più costoso; è definita anche manutenzione “a guasto” in quanto viene effettuata solo dopo la comparsa di una situazione di rottura. È quella che nell’immaginario si definisce “la peggiore” in quanto si associa quasi sempre ad un arresto imprevisto della produzione.
Chiaramente comporta delle conseguenze, tra cui:
- Costi elevati sia di materiali che di servizi manutentivi che non possono essere contrattati a causa delle tempistiche.
- Improvvisa perdita di produzione.
- Rischio di grave danneggiamento del macchinario.
- Infortuni al personale.
- Ritardi di consegna ai clienti.
- Operatori inattivi fino alla risoluzione del guasto, almeno in parte.
Manutenzione preventiva
In questo caso l'intervento è volto a prevenire il guasto secondo criteri prestabiliti. La manutenzione avviene a seguito dell’individuazione e della misurazione di uno o più parametri e dell’indicazione del tempo residuo prima del guasto, secondo modelli appropriati. In altri termini, si pone l’obiettivo di prevenire il deterioramento dei componenti, prolungarne la vita e regolarizzarne la manutenzione. Prevedibilmente richiede un elevato livello di competenza e specializzazione dei manutentori. Per dare visibilità a questo sistema, si imposta un piano di manutenzione che definisce le azioni periodiche necessarie, specificando per ognuna i componenti e le parti della macchina su cui intervenire, i contenuti e le modalità di intervento (metodi, attrezzi, parametri […]), l’operatore responsabile, la frequenza. Questa modalità consente di ridurre la probabilità che la macchina o un suo componente non siano in condizioni operative accettabili.
Questa tipologia di manutenzione può essere:
- A intervalli regolari.
- A intervalli sicuri.
- A intervalli irregolari.
- A età costante.
- A data costante.
- Di routine.
- Straordinaria.
Manutenzione predittiva
Definita anche “secondo condizione”, la manutenzione predittiva viene effettuata attraverso controlli di routine o continui e si basa su due assunti:
- Molti guasti non accadono istantaneamente.
- È possibile individuare la nascita e l’evoluzione di un guasto.
In altri termini, le macchine restituiscono degli avvertimenti prima di guastarsi, definibili come “guasti potenziali”. Quindi, il manutentore che conosce bene lo stato reale dei singoli componenti della macchina, può intervenire preventivamente e in modo razionale. È di difficile applicazione ma l’evoluzione tecnologica sta rendendo disponibili strumenti e modelli di calcolo sempre più affidabili e dai costi relativamente contenuti.
Manutenzione opportunistica
È un tipo di manutenzione molto diffusa e talvolta gestita in modo quasi inconsapevole. È così definita perché interviene durante una riparazione o in un'altra occasione in cui il macchinario non è operativo. Generalmente infatti, in questi casi, si sostituiscono anche altri componenti che migliorano il livello di affidabilità del sistema oppure durante la riparazione si rilevano segnali di marcato degrado (o addirittura rottura) di altri componenti e si procede quindi alla loro riparazione/sostituzione. In questo secondo caso si rientra nelle stesse problematiche descritte per la manutenzione “a guasto”.
Quanto argomentato sino ad ora dovrebbe condurci alla riflessione che in realtà per quanto onerose siano le azioni manutentive, quanto più si è in grado di agire in maniera tempestiva tanto più si potranno evitare danni o rallentamenti.
Inoltre, si deve considerare che il concetto stesso di Manutenzione si sta evolvendo superando il pregiudizio di essere una mera azione riparativa.
TPM - Total Productive Maintenance
Come anticipato rappresenta l’evoluzione del concetto di manutenzione. Di cosa si tratta? In Italia la sua traduzione è “manutenzione produttiva totale” e può essere definita, nello specifico, come l’evoluzione della Manutenzione Preventiva. È quindi un approccio alla manutenzione, un sistema produttivo che punta al raggiungimento del miglioramento dell’efficienza aziendale nella sua globalità.
Le fondamenta su cui poggia è l’ambizione di arrivare a Zero incidenti, Zero difetti e Zero guasti.
Poiché l’obiettivo ultimo non è “riparare” ma rendere l’impresa competitiva, è chiaro che deve esserci il coinvolgimento di una pluralità di attori aziendali. La responsabilità della manutenzione degli impianti è quindi estesa a più livelli, non solo quindi ai manutentori. Ricade soprattutto sulle spalle degli operatori diretti che sono coinvolti nella manutenzione in progetti di miglioramento e in riparazioni semplici, ossia tutte le attività che diventano parte della loro routine.
Il TPM si basa quindi sul coinvolgimento totale delle persone e sulla prevenzione come principale strumento di eliminazione delle perdite.
Questo sistema produttivo, inoltre, si fonda su due pilastri fondamentali. Uno è quello della Autonomous Maintenance, o manutenzione autonoma, l’altro è la Workplace Organization.
L ’applicazione di queste due metodologie comporta miglioramenti in termini di:
- Riduzione sprechi.
- Riduzione scarti di produzione.
- Incremento produttività.
- Sensibilizzazione e miglior coinvolgimento del personale.
- Ordine e spazio delle aree di lavoro.
- Minore rischio infortuni.
- Migliore predisposizione al lavoro di team.
La WO è sicuramente importante e per molte aziende rappresenta a tutti gli effetti il primo passo verso il cambiamento.